Bhel Haridwar Training Report Block 3 Pdf
Training report submitted to CFFP, BHEL Haridwar as part of. I am extremely grateful to Bharat Heavy Electricals Limited, Haridwar. Travelling block. 136045679 BHEL Haridwar Block 3 Turbine Manufacturing Training Report (1) - Download as Text File (.txt), PDF File (.pdf) or read online. TABLE OF CONTENTS CHAPTER 1- INTRODUCTION ON B.H.E.L. CHAPTER 2- BLOCK 4 CIM SHOP CHAPTER 3-MANUFACTURING PROCESS OF 600MW TG STATOR BARS CONCLUSION CHAPTER 1 INTRODUCTION ON BHEL Bharat Heavy Electricals Limited (BHEL) is an Indian integrated power plant equipment manufacturer.
Turbo Generators & Exciters BHEL Haridwar, Production Block-1, HEEP,Ask Latest information,Abstract,Report,Presentation (pdf. For training report of block 3.
-Combination punch, shear and bar cutters, circular saws and bar shears are used for cutting angles, shapes, flats and rods. B) Straightening Rollers are used for straightening plates and large sized blanks and a 160 ton friction press for straightening small sized blanks. A roll bending machine is used for straightening and bending rolled beams and angles. C) Hydraulic bending press of 800 ton and 400 ton and a 250 ton friction press are used for cold and hot bending from rolled sheets and shapes. Parts to bend are pre heated in a 700 KW electric furnace, when ever needed. D) Finished parts are inspected at the working place.
Some of the on-going development & demonstration projects include: Smart wall blowing system for cleaning boiler soot deposits, and micro-controller based governor for diesel-electric locomotives. The company is also engaged in research in futuristic areas, such as application of super conducting materials in power generations and industry, and fuel cells for distributed, environment-friendly power generation.
In 1982, it entered into power equipments, to reduce its dependence on the power sector. It developed the capability to produce a variety of electrical, electronic and mechanical equipments for all sectors, including transmission, transportation, oil and gas and other allied industries. In 1991, it was converted into a public limited company.
The product resulting from (the process of) fabrication may be called a fabrication. PROCESS:- Processes involved in Fabrication are:- Cutting & Burning. Forming Machining. APPLICATIONS:- Equipment for Industrial Applications. Equipment for Specialty Gases Applications.
Power, Transmission, Industry, Transportation, Renewable Energy, Oil & Gas and Defence.BHEL has 15 manufacturing divisions, two repair units, four regional offices, eight service centres, eight overseas offices and 15 regional centres and currently operate at more than 150 project 4 5. Sites across India and abroad. BHEL places strong emphasis on innovation and creative development of new technologies. Our research and development (R&D) efforts are aimed not only at improving the performance and efficiency of our existing products, but also at using state-of-the-art technologies and processes to develop new products. This enables us to have a strong customer orientation, to be sensitive to their needs and respond quickly to the changes in the market. The high level of quality & reliability of our products is due to adherence to international standards by acquiring and adapting some of the best technologies from leading companies in the world including General Electric Company,Alstom SA, Siemens AG and Mitsubishi Heavy Industries Ltd., together with technologies developed in our own R&D centres.
ELECTRICAL MACHINES: DC general purpose and rolling mill machines from 100 to 19000KW suitable for operation on voltage up to 1200V. These are provided with STDP, totally enclosed and duct ventilated enclosures. DC auxiliary mill motors. CONTROL PANEL: Control panel for voltage up to 400KW and control desks for generating stations and EMV sub–stations. CASTING AND FORGINGS: Sophisticated heavy casting and forging of creep resistant alloy steels, stainless steel and other grades of alloy meeting stringent international specifications. DEFENCE: Naval guns with collaboration of Italy. DEFINATION:- 2.
Normal oxygen fuel gas or arc processes can be used to produce rapid melting and metal removal. 28 • Manual metal arc Gouging is a process in which a process a electrical arc is generated to melt the material. Other techniques like special electrodes or a jet of compressed air are used to blow away the molten material. No specific high purity or compressed gases are needed in these processes.
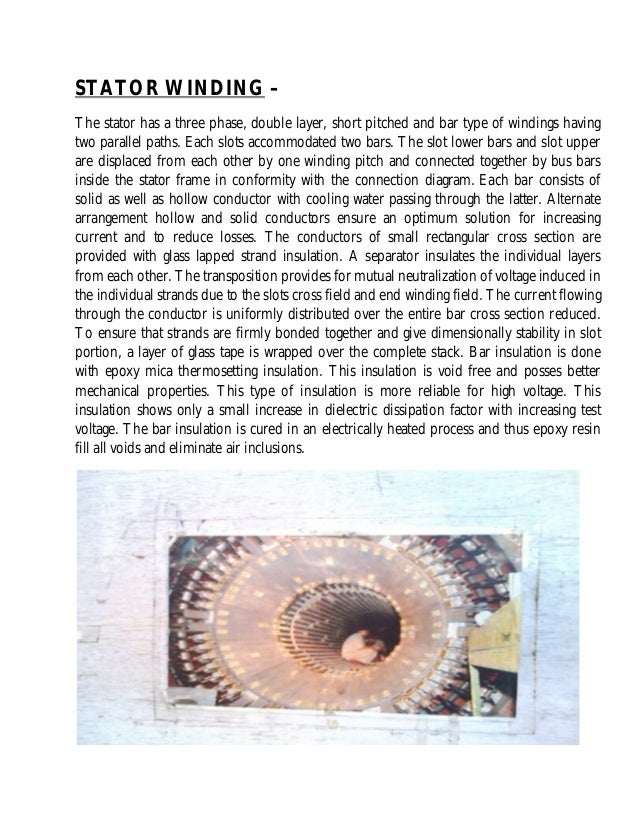
Training Report Form
Business should uphold the freedom of association and the effective recognition of the right to collective bargaining; 4. The elimination of all form of forces and compulsory labor. The effective abolition of child labor, and 6.
B) Cold bending of pipes is carried out on a pipe bending machine. Bending of carbon and alloy steel pipes of 114 mm dia. And above is performed by heating them in electric furnaces and then by hot bending. 44 • c) Facing of pipes and beveling for welding is carried out on a horizontal boring machine with portable type pipe chamfering machine.
Presently a 400 kV FACTS (Flexible AC Transmission System) projects is under execution. The range of system & equipment supplied includes: captive power plants, co-generation plants DG power plants, industrial steam turbines, industrial boilers and auxiliaries.
If the echo is recorded with disturbance earlier than the other end then the job is defective. 30 • FIG.10 DEFECT DETECTED BY ULTRA SONIC FAULT DETECTOR 31 • 7. MACHINING Machining can be defined as the process of removing material from a work piece in the form of chips.The term metal cutting is used when the material is metallic. Most machining has very low set-up cost compared to forming, molding, and casting processes. However, machining is much more expensive for high volumes.
Carriage or ring is mounted on the table with the help of fixture and then guide blade carrier blade is weld to the inner ring to both side of curved surface by tilting the table 7.3.2 MACHINE SPECIFICATION a) Gross weight = 7600 kg. B) Size =393*383*180 cm3.
1.Vocational Training Report Turbine Blade Shop-Block 3 Bharat Heavy Electricals Limited Ranipur,Haridwar (Uttrakhand) Submitted By: Submitted To: Yuganter Rawat Mr.Hitendra Bankoti B-Tech 3rd year Amrapali Institute of technology and science,Haldwani 1 2. ACKNOWLEDGEMENT “An engineer with only theoretical knowledge is not a complete engineer. Practical knowledge is very important to develop and apply engineering skills”. It gives me a great pleasure to have an opportunity to acknowledge and to express gratitude to those who were associated with me during my training at BHEL.
I am very great-full to Mr. Meena for providing me with an opportunity to undergo training under his able guidance.
In Oxy-fuel cutting, a cutting torch is used to heat up ferrous metal to kindling temperature (about 980°C). A stream of pure oxygen is trained on the hot metal which chemically combines with the iron which then flows out of the cut, or kerfs, as an iron-oxide slag. There have been examples of oxy-hydrogen cutting sets with small (scuba sized) gas cylinders worn on the user's back in a backpack harness, for rescue work. BENDING Bending is a process by which metal can be deformed by plastically deforming the material and changing its shape. The material is stressed beyond the yield strength but below the ultimate tensile strength. The surface area of the material does not change much. Bending usually refers to deformation about one axis.
Along with above a blow of argon gas is passed through holder to provide inert atmosphere at welding. The strength of TIG welding is more than any other type of welding.
1 E N V I R O N M E N T A L P O L I C Y 8 1. 2 O C C U P A T IO N A L H E A LT H A N D S A FE T Y P O L IC Y 8 1.
GOUGING:- Thermal gouging is an essential part of welding fabrication. Used for rapid removal of unwanted metal, the material is locally heated and molten metal ejected usually by blowing it away.
1 P O W E R G E N E R A T I O N 3 1. 2 P O W E R T R A N S M I S S I O N & D I S T R I B U T I O N 3 1.
The resulting 36 • work piece may then be used 'between centers' in another operation. The usage of the term metal lathe may also be considered somewhat outdated these days, plastics and other composite materials are in wide use and with appropriate modifications, the same principles and techniques may be applied to their machining as that used for metal.
Not avl The Central Foundry Forge Plant (CFFP) is engaged in manufacture of large size Castings and Forgings of various types of steels like alloy steels, creep resistant steel and supercritical grade steel. Not avl The Pollution Control Research Institute (PCRI) provides services in the field of Environmental Management and Pollution Control in the areas of air, water, noise and solid waste. Not avl HEEP & CFFP both have been awarded certificates forQuality Systems (ISO-9001:2008) Environment(ISO-14001) and Occupational Health & Safety (ISO-18001) not avl HEEP is the only Public Sector unit in India to have won the CII-EXIM Bank Prize for Business Excellence (2006). You have selected one or more posts to quote.
23 • FIG.4 CNC BACK PRESS MACHINE 4.2. ROLLING MACHINE:- THREE ROLL BENDING MACHINE: Roll benders use three rolls (typically) to bend solids, extrusions and tube and pipe to various diameters by adjusting one or two rolls. The pyramid style roll benders have one moving roll, usually the top roll. Double pinch type roll benders have two adjustable rolls, usually the bottom rolls, and a fixed top roll. Large arcs, circles and spirals are typical applications for roll benders. The roll bending machine in BHEL has following specifications:- S.R.NO. SPECIFICATIONS MAXIMUM WORKING LENGTH MINIMUM DIAMETER OF FORMING PLATE THICKNESS UPPER ROLL DIAMETER DIMENSIONS 8000 MM 1300 MM 32 MM 7550 MM 24 • 5.
In a reheat turbine, steam flow exits from a high pressure section of the turbine and is returned to the boiler where additional superheat is added. The steam then goes back into an intermediate pressure section of the turbine and continues its expansion. Casing or Shaft Arrangements Turbine arrangement features two or more shafts not in line driving two or more generators that often operate at different speeds. A cross compound turbine is typically used for many large applications. Principle of Operation and Design An ideal steam turbine is considered to be an isentropic process, or constant entropy process, in which the entropy of the steam entering the turbine is equal to the entropy of the steam leaving the turbine. No steam turbine is truly “isentropic”, however, with typical isentropic efficiencies ranging from 20%- 90% based on the application of the turbine. The interior of a turbine comprises several sets of blades, or “buckets” as they are more commonly referred to.
A cross compound Steam turbines are made in a variety of sizes ranging from small 1 hp (0.75 kW) units (rare) used as mechanical drives for pumps, compressors and other shaft driven equipment, to 2,000,000 hp (1,500,000 kW) turbines used to generate electricity. There are several classifications for modern steam turbines.
Situate in Ranipur near Haridwar, the Bharat Heavy Engineering Limited employs over 8,000 people. BHEL is an integrated power plant equipment manufacturer and one of the largest engineering and manufacturing companies in India in terms of turnover.
34 • c) Table diameter = 3500mm (without extension), 4500mm (with extension). D) Rotation of table = 00 to 3600 (clockwise or anti clock) e) Tilting of table = 00 to 1350. F) Table rotation speed = 0.012-0.5 rpm. FIG.13 MANIPULATOR HOLDING GBC (GUIDE BLADE CARRIER) 7.4. COPY MILLING MACHINE This machine is designed for milling profiles or relief contours (three-dimensional milling) on articles made of various materials by means of a cutting tool (milling cutter), which reproduces on the article the surface or contour of a master device—for example, a master cam in the shape of a flat template, a three-dimensional model, or a contour drawing. The master device is mechanically, pneumatically, or hydraulically connected to a servomechanism, which directs the cutting tool. 35 • The servomechanism acts on an amplifying device on the one hand and, on the other hand, on an actuating device.
One set of stationary blades is connected to the casing and one set of rotating blades is connected to the shaft. The sets intermesh with certain minimum clearances, with the size and configuration of sets varying to efficiently exploit the expansion of steam at each stage. Turbine Efficiency To maximize turbine efficiency, the steam is expanded, generating work, in a number of stages. These stages are characterized by how the energy is extracted from them and are known as impulse or reaction turbines. Most modern steam turbines are a combination of the reaction and impulse design.
HYDRAULIC PRESS:- A hydraulic press is a hydraulic mechanism for applying a large lifting or compressive force. It is the hydraulic equivalent of a mechanical lever, and is also known as a Bramah press after the inventor, Joseph Bramah. Hydraulic presses are the most commonly-used and efficient form of modern press.
The distance the large piston will move is the distance that the small piston is moved divided by the ratio of the areas of the heads of the pistons. There were two hydraulic presses at present which are: CNC Back Press-340 ton. Manually operated- 400 ton, 800 ton.
This process is used to prevent automated posts. Possibly Related Threads. Thread: Author Replies: Views: Last Post Guest 0 07:30 PM: Guest Guest 0 12:51 AM: Guest Guest 0 12:51 AM: Guest Guest 0 12:51 AM: Guest Guest 0 03:12 PM: Guest Guest 530 03:19 PM: Guest Guest 0 09:09 PM: Guest Guest 0 07:59 PM: Guest Guest 394 03:47 PM: nnktaker Guest 0 10:57 AM: Guest This Page May Contain What is bhel haridwar block 3 ppt And Latest Information/News About bhel haridwar block 3 ppt,If Not.Use to get more info about bhel haridwar block 3 ppt Or.
Inspection of weld quality and flaw detection is carried out by means of X-ray machines, gamma-grapy machines of cobalt and iridium isotopes and ultrasonic flaw detectors. Pressure vessels that are boilers, heaters, condensers and coolers undergo hydraulic tests on special test beds meant for hydraulic testing. Kerosene leakage test is also done in case of thin walled vessels. Process being followed in pipe section is mentioned below: a) Pipes with diameter of 10-60 mm and 38-108 mm are cut on pipe cutting machines and oxy-acetylene cutters.
It is less pure which causes repeated cleaning of burner. The gap between Nozzle & plate is 5mm.
A higher purity level means a higher cutting speed. Oxy-fuel cutting are processes that use fuel gases and oxygen to either weld or cut metals.
You have selected one or more posts to quote. Image Verification (case insensitive) Please enter the text within the image on the left in to the text box below.
ALOK SHUKLA Sir. I am also grateful to the management of Bharat Heavy Electricals Limited (B.H.E.L.), Haridwar for permitting me to have training during 17th June to 31st July, 2013. We worked as a team and saw ups and downs which are part of any project work. But in the end it was their Guidance and my team work which made this project possible. Last but not the least we would also like to thank all our teachers & friends for their constructive criticism given in right spirit. Abhishek Kumar () 7th Semester, B.Tech. Department of Mechanical Engineering Greater Noida Institute Of Technology, Greater Noida • ABSTRACT In the era of Mechanical Engineering, Turbine, A Prime Mover ( Which uses the Raw Energy of a substance and converts it to Mechanical Energy) is a well known Machine most useful in the the field of Power Generation.
B) DIAPHRAGM SECTION: Welded diaphragms of steam turbines are assembled, welded and stress relieved in this section. 41 • c) COOLERS SECTION: In this section tubes of coolers are cut to the required size, then turned and thereafter winding and soldering of spirals on tubes is carried out by automatic machines. These are then assembled to form coolers which are then assembled and hydraulically tested. MANUFACTURING PROCESSES Manufacturing starts with Preparation of individual parts before assembly, in Bay -1. A) The metal is first marked and cut by the following machines:- - Guillotine Shearing machine for cutting and trimming steel sheets and plates up to 25mm thick with straight contours. -Stationary and portable Oxy-acetylenecutting machines for cutting machines for cutting parts out of steel plates.